Jesse Brown
SmokeStack
A device to integrate great smoke flavor with the familiar grilling process
Skills
-
Research and Development
-
Sheet Metal Work
-
Sheet Metal Design
-
3D Printing
-
Performance Testing
Senior Capstone
Problem
Our client from a large US grilling company challenged us to create a device to introduce real smoke flavor into the traditional grilling environment. Our goal was to create an easy-to-use device that adds smoke flavor with real smoke to foods grilled on a gas or electric grill.
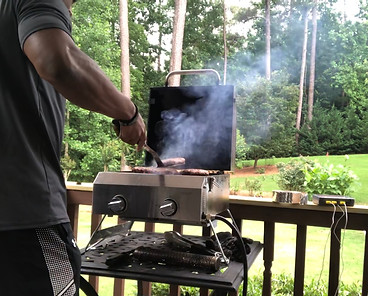
Requirements
The solution needs to...
-
provide a positive user experience
-
impart a pleasant smoke flavor using real smoke
-
be compatible with both gas and electric grills
- not interfere with typical grilling temperatures
Process

We started this project focused on learning about smoking and existing products that attempt to achieve similar functions. A function tree was created to itemize our discoveries into system goals for a functional prototype. We reached out to potential users via online surveys to poll their expectations and wants from this type of product.

Testing in the first half of the project was conducted to lock in the parameters needed impart the best smoke flavor efficiently. We determined this function as being the critical system of the entire process. The results helped us begin mapping solutions to each function on the function tree.

Brainstorming led to the creation of an concept selection matrix to organize the ideas for the initial evaluation stages. Each concept was evaluated on a number of criteria measuring aspects such as feasibility and function fulfillment. Storyboarding was used to explore use cases of each concept.

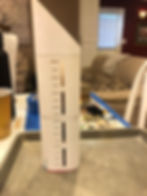

More testing and evaluations led us to narrowing down to a single alpha prototype concept. From here, we developed the features to optimize performance. Being remote, many of the design tests were conducted using 3D printed parts.
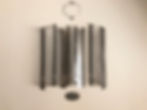
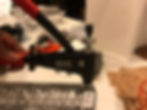

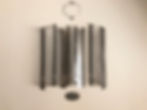
Once all parameters were finalized, we had the Solidworks Sheet Metal model sent to be water jet cut out and bent for functional tests. Due to prototyping limitations, this model for testing had minor form factor modifications. I assembled the parts and tested the prototype.
Role



Result
Although remote study situations did not allow us to be able to prototype and test in ways we hoped to, we were able to design a practical system. We were able to deliver a functional modified metal prototype as well as an accurate 3D printed model of the system and its interactions accompanied with specifications for producing a grill ready product.
I led the prototyping and testing efforts our team made on this project. During the remote phase of the project, I was able to conduct the appropriate performance testing and communicate that information clearly to the rest of the team virtually.

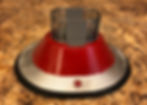

